For about two years, we have been searching for a supplier of adobe bricks.
Mostly, I love doing everything ourselves, but fencing 40 acres and making our own adobe were two things I’d rather not do.
So we pursued numerous avenues. There was a guy who would come make bricks right on our property that we were excited about. Except that he never seemed to be able to come out here and the price kept going up. Then rumor had it that there were a couple local suppliers. None seemed to be in business anymore. Of course, there was the route that several people we knew took of getting bricks in little batches from Mexico, but the stories of how that went were too terrible to recount here.
Finally, about a month ago, Brad found New Mexico Earth Adobes in Albuquerque who said they’d make and deliver bricks. Delivery is always a big problem here, and especially with adobe which is very, very heavy and not economical to ship. Just a few weeks ago, this place had a “sale” on bricks, and so we jumped on it. Delivery was all set, and we upped our order to a whole truckload.
The driver was scheduled to arrive at 6am this morning.
At 5am, our alarm went off. A minute or two later, Brad said, “I hear the truck.” It was pitch black.
We dressed hurriedly and got ready to receive. Our friend who helped us forklift the vigas had also agreed to help unload this truck, because the driver wasn’t permitted to bring a forklift into AZ (the many-eth time we’ve had cross-state permit issues.) He wasn’t scheduled to be there until 6 so Brad went out to see the driver.
Next problem — this was the 2nd truck that couldn’t get in our driveway. (Perhaps not coincidentally, they were two of our largest and heaviest deliveries.) The 70+ foot truck wasn’t a problem, but he had an enormous sleeper cab that wouldn’t make the turn into the gate without taking out a post.
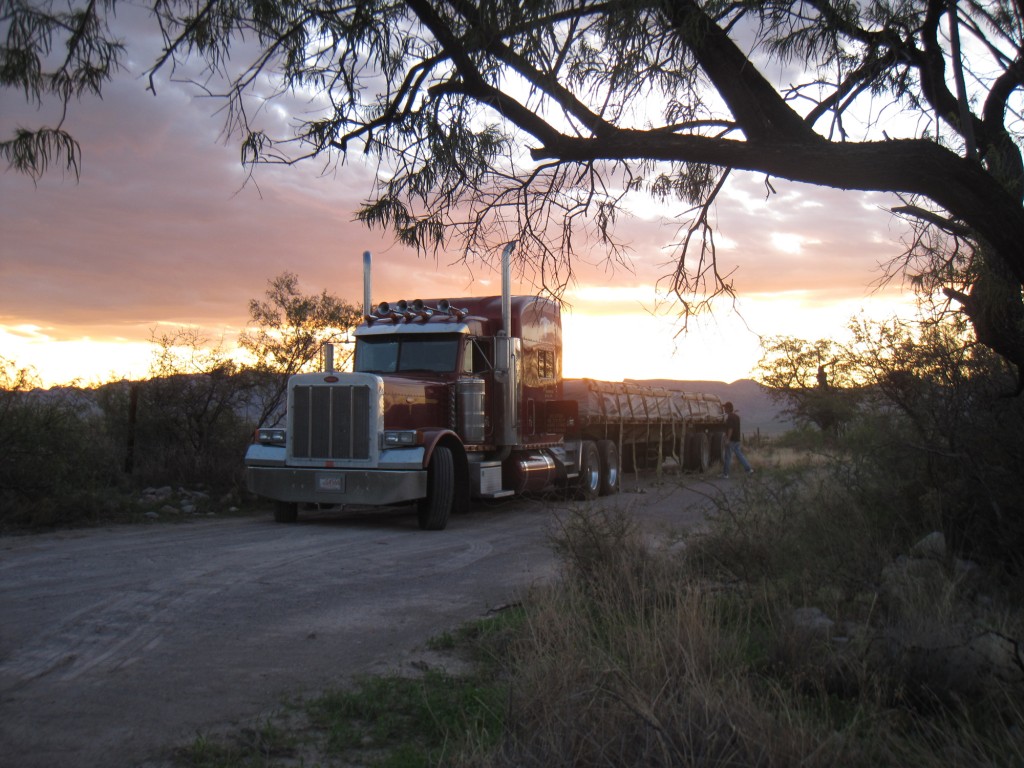
So….we adjusted plans and decided to unload all the bricks at the front gate and then to transfer them up to the house.
Another issue, but one we already knew about, was that our friend’s forklift couldn’t lift the 2500 pounds that each pallet would normally weigh. The company agreed to pack them at 2000 pounds (at no charge beyond the extra pallets – much appreciated), but even that seemed a little heavy, so Brad and I transferred about 12 bricks from each pallet to some extra pallets we had. They weigh about 30 pounds each. That is a lot of weight to move by hand, and as we did it, I knew that this was only the first of many times we’d undoubtedly be moving these by hand. (Who needs a gym?)
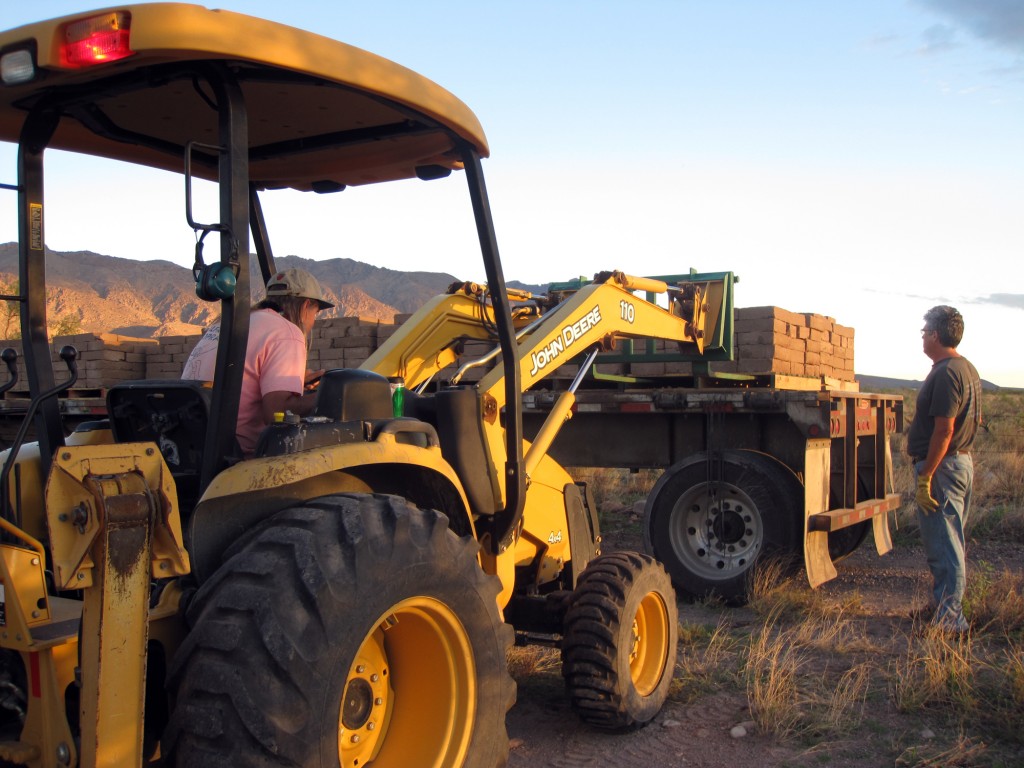
All went well. Here’s the truck before and after:
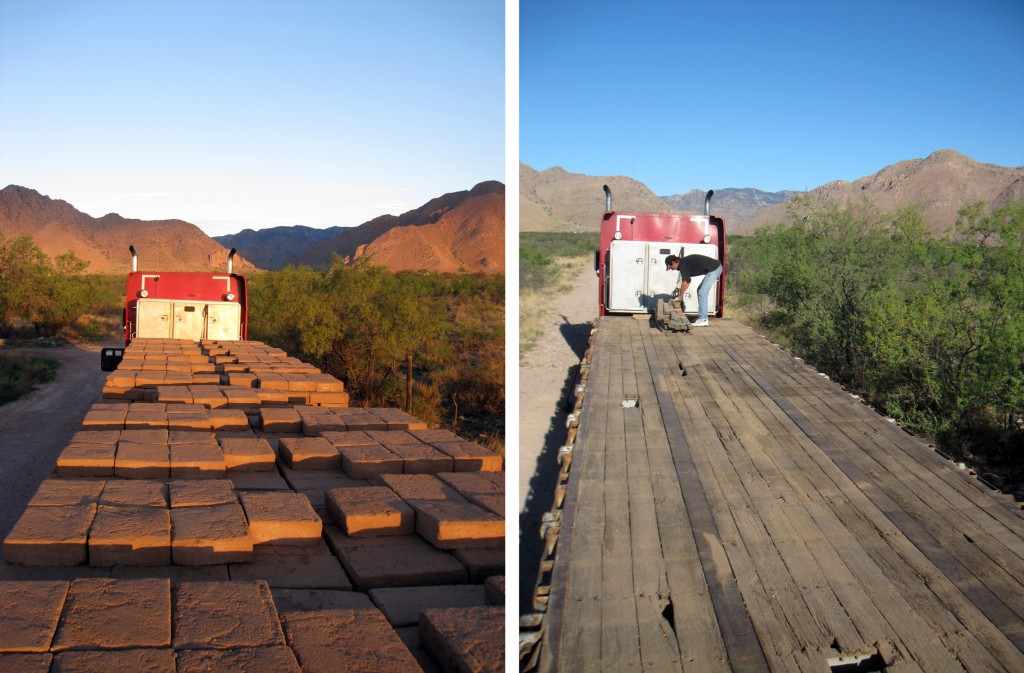
And here’s the staging area at the front gate.
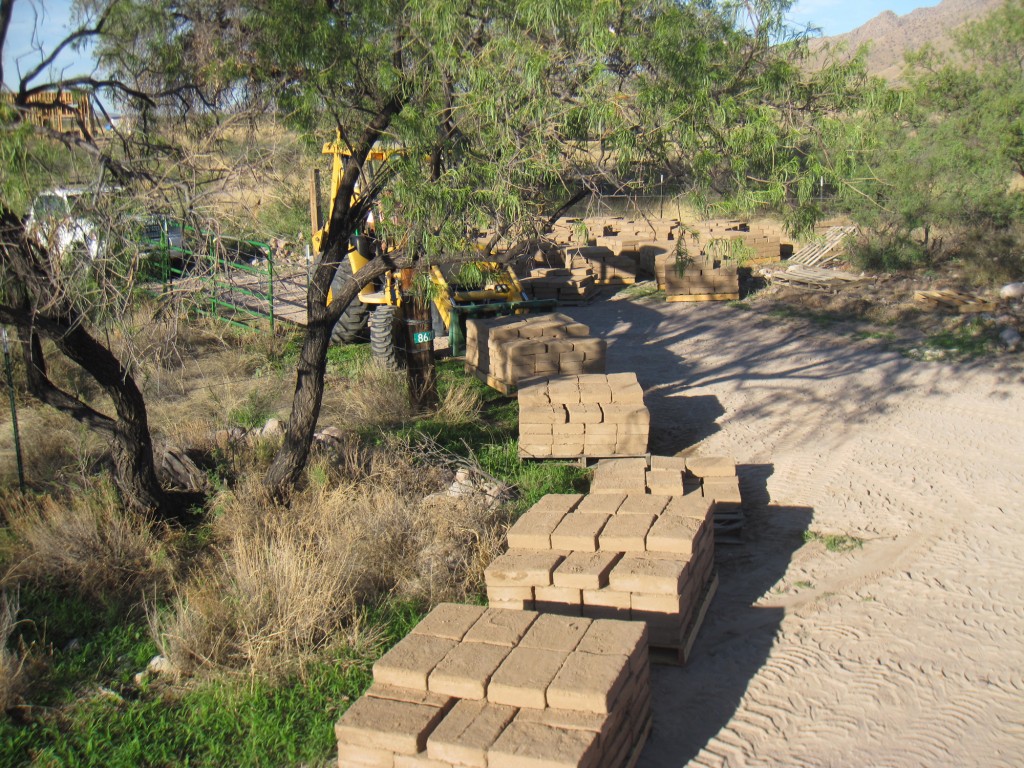
And finally in their temporary storage spot (where our lovely patio will one day be). This picture also gives a good idea of the proximity of the two houses.
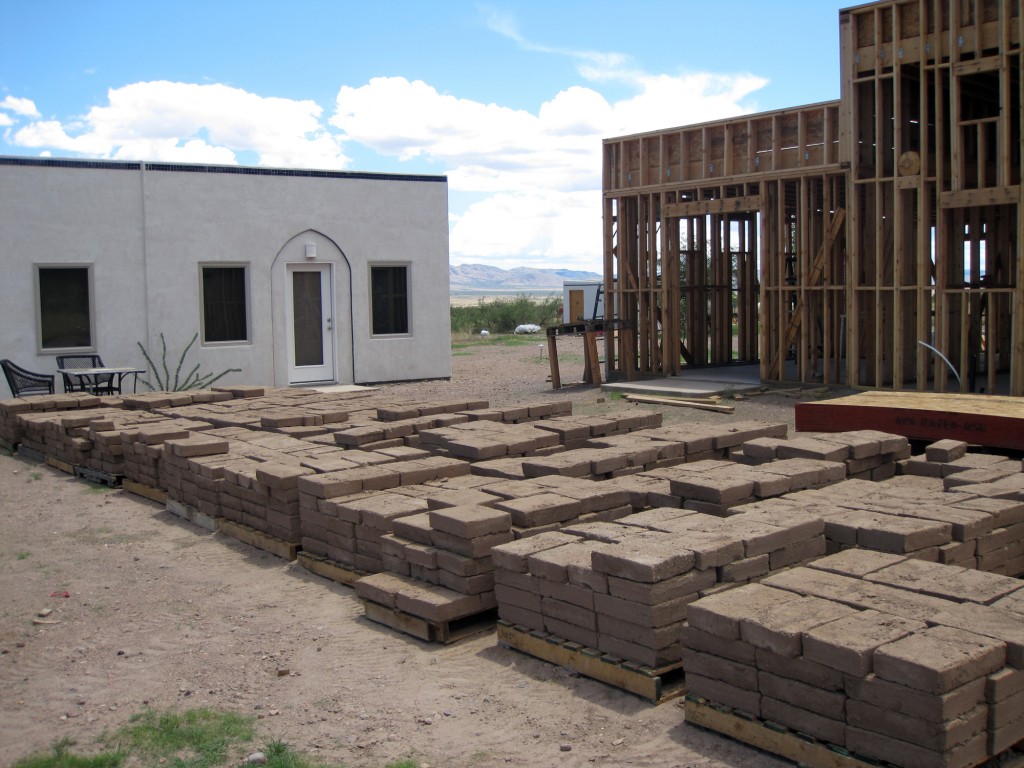
The bricks are lovely, very uniform and durable. We broke almost none in the various moves today (and we’ve seen adobe bricks that broke if you sneezed and melted in the rain — these are stabilized though.)
It will likely be some time before we start building with this. We have to get the whole house covered and electrical in first. It’s great to have this looming procurement challenge behind us though.